Plastikozko piezak nola diseinatu
Deskribapen laburra:
To diseinatu plastikozko piezakpiezen forma, tamaina eta zehaztasuna zehaztea da, piezak produktuan betetzen duten paperean eta plastikoa moldatzeko prozesuaren arauan oinarrituta. Azken irteera moldea eta plastikozko pieza fabrikatzeko marrazkiak dira.
Produktuen fabrikazioa diseinuarekin hasten da. Plastikozko piezak diseinatzeak zuzenean zehazten du produktuaren barne egitura, kostua eta funtzioa gauzatzea, eta moldearen ekoizpenaren, kostuaren eta zikloaren hurrengo urratsa zehazten du, baita injekzioa eta prozesatzeko prozesua eta kostua ere.
Plastikozko piezak asko erabiltzen dira gizarte modernoaren hainbat produktu, instalazio eta pertsonen bizitzan. Plastikozko piezek forma eta funtzio desberdinak behar dituzte. Material plastikoak erabiltzen dituzte eta haien propietateak askotarikoak dira. Aldi berean, industrian plastikozko piezak egiteko modu asko daude. Beraz, plastikozko piezak diseinatzea ez da lan erraza.
Pieza desberdinen diseinua eta materiala prozesamendu desberdinak sortzen dira. Plastikoa moldatzeko prozesuak honako hauek biltzen ditu batez ere:
1. injekzio moldaketa
2. putzuen moldaketa
3. konpresio moldaketa
4. biraketa moldaketa
5.termoformaketa
6. estrusioa
7.fabrikazioa
8.sumina
Masa ekoizteko modu ugari daude. Injekzio bidezko moldaketa fabrikazio metodo ezaguna da, injekzio bidez moldatutako% 50 ~% 60 plastikozko piezak injekzio bidezko moldaketa bidez ekoizten direlako, abiadura handiko ekoizpen gaitasuna da.
Diseinatu ditugun plastikozko pieza batzuen erakusleihoa:
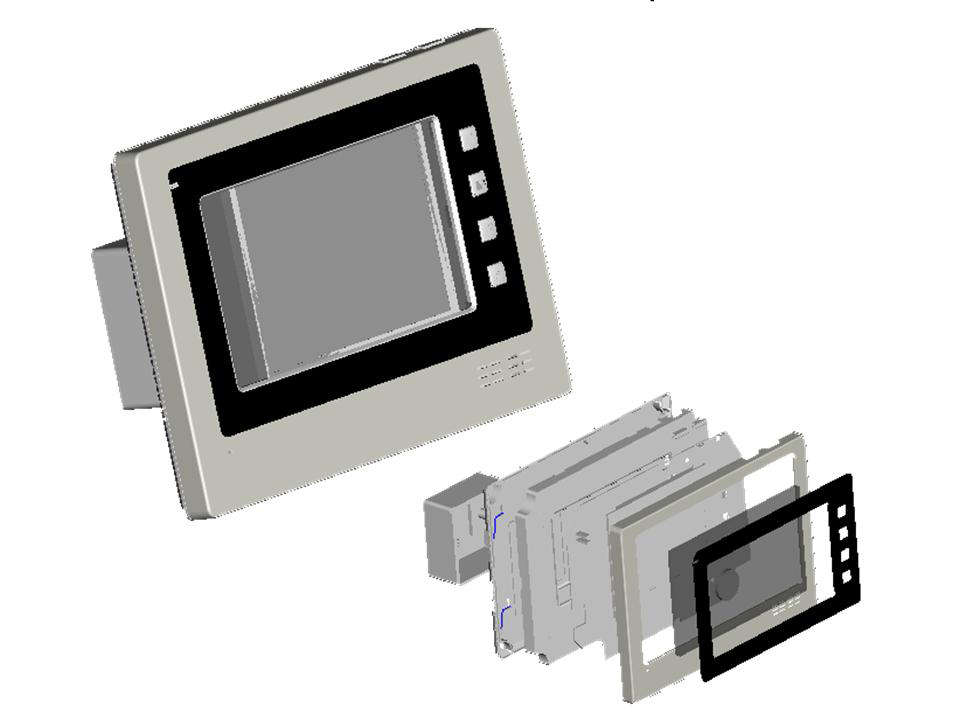
Ikusteko telefonoaren plastikozko itxitura
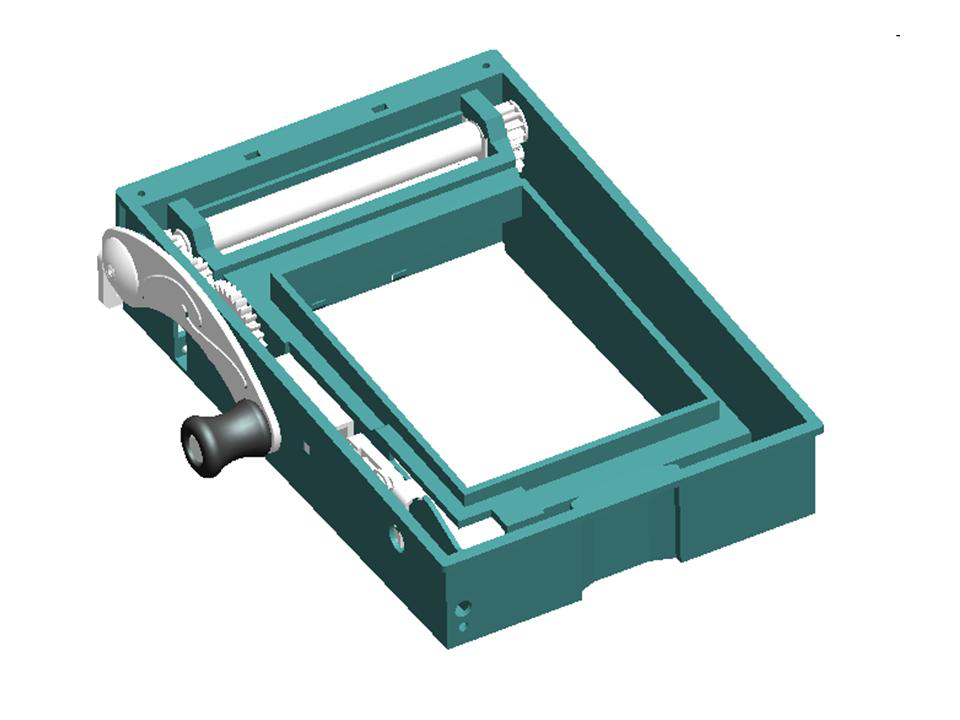
Mekanismoaren zati plastikoak
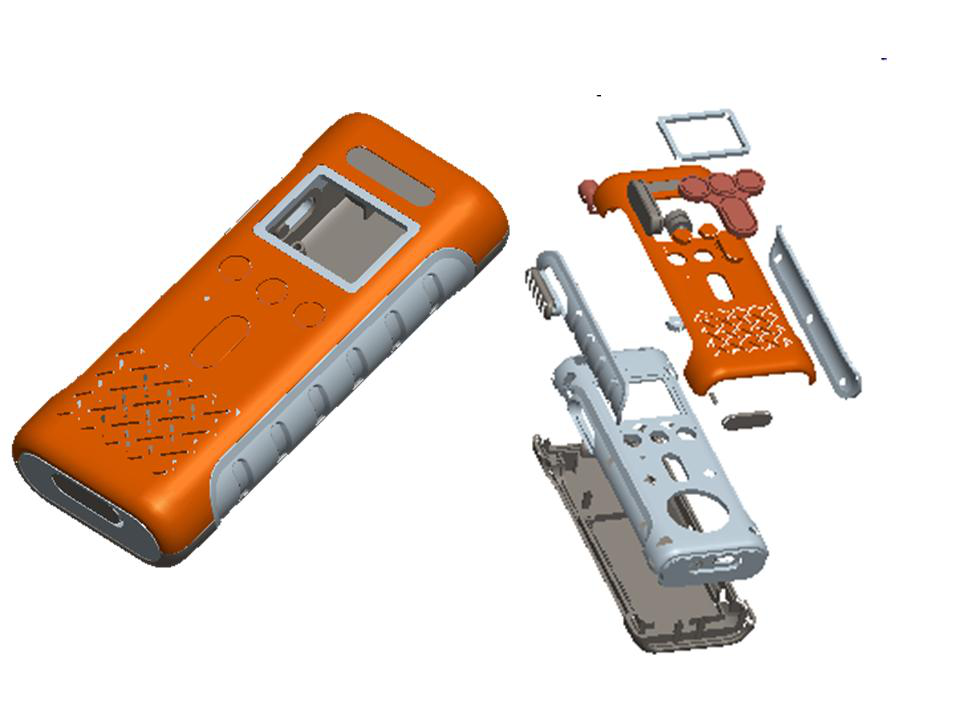
Plastikozko kaxa elektronikoak
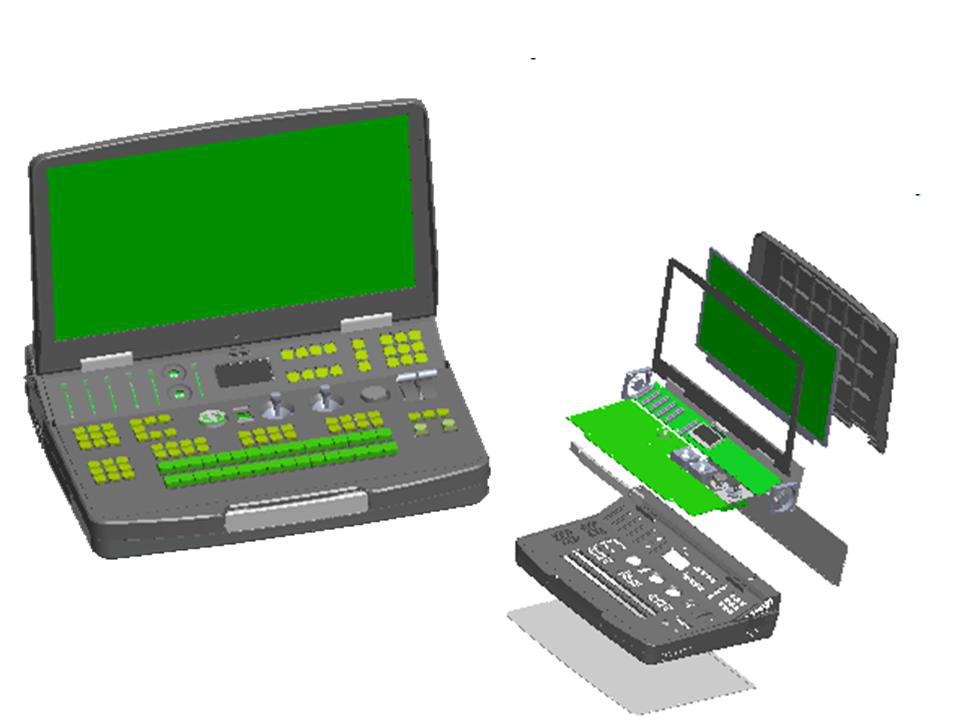
Instrumenturako plastikozko karkasa
Jarraian plastikozko piezak hiru alderditan nola diseinatu zehazten ditugu
* Ezagutu behar dituzun plastikozko piezak diseinatzeko 10 aholku
1. Zehaztu itxuraren diseinua eta produktuaren tamaina.
Hau da diseinu prozesu guztiaren lehen urratsa. Merkatu ikerketen eta bezeroen eskakizunen arabera, zehaztu produktuen itxura eta funtzioa eta formulatu produktuak garatzeko lanak.
Garapen zereginaren arabera, garapen taldeak bideragarritasun analisi teknikoa eta teknologikoa egiten dio produktuari, eta produktuaren 3D itxura eredua eraikitzen du. Ondoren, funtzioaren errealizazioaren eta produktuaren muntaiaren arabera, pieza posibleak aurreikusten dira.
2. Bereizi banakako piezak produktuen marrazkietatik, aukeratu plastikozko erretxina mota plastikozko piezetarako
Urrats hau zatiak aurreko urratsean lortutako 3D eredutik bereizteko eta banaka diseinatzeko da. Piezen eskakizun funtzionalen arabera, aukeratu plastikozko lehengai edo hardware material egokiak. Adibidez, ABS normalean erabiltzen da
oskolak, ABS / BC edo PCak zenbait propietate mekaniko izan behar dituzte, zati gardenak, hala nola, pantaila, farola PMMA edo PC, engranaje edo POM edo Nylon higadurako piezak.
Piezen materiala hautatu ondoren, xehetasunen diseinua has daiteke.
3. Zehaztu zirriborroen angeluak
Zirriborroaren angeluak plastikoa moldetik ateratzeko aukera ematen du. Zirriborro angelurik gabe, piezak erresistentzia handia eskainiko luke kentzean marruskaduraren ondorioz. Zirriborro-angeluak piezaren barrualdean eta kanpoaldean egon behar dira. Zatia zenbat eta sakonagoa izan, orduan eta handiagoa da zirriborroaren angelua. Arau soil bat hazbeteko 1 graduko zirriborro angelua edukitzea da. Zirriborro angelu nahikorik ez izateak zatiaren alboetan marradurak eta / edo ejecting pin marka handiak sor ditzake (gehiago jakingo duzu aurrerago).
Zirriborroa kanpoko gainazalaren angeluak: zenbat eta sakonagoa izan, orduan eta angelu handiagoa dago. Arau soil bat hazbeteko 1 graduko zirriborro angelua edukitzea da. Zirriborro angelu nahikorik ez izateak zatiaren alboetan marradurak eta / edo ejecting pin marka handiak sor ditzake (gehiago jakingo duzu aurrerago).
Normalean, itxura ona duen gainazala izateko, ehundura piezen gainazalean egiten da. Ehundura duen horma latza da, marruskadura handia da eta ez da erraza barrunbetik ateratzea, beraz marrazteko angelu handiagoa behar da. Ehundura zakarragoa da marrazketa angelu handiagoa behar duena.
4. Definitu hormaren lodiera / lodiera uniformea
Forma solidoa moldatzea ez da nahi injekzioan, arrazoi hauek direla eta:
1) .Hozte denbora hormaren lodieraren karratuaren proportzionala da. Solidoak hozteko denbora luzeak masa ekoizpenaren ekonomia garaituko du. (beroaren eroale eskasa)
2). Sekzio lodiagoa atal meheagoa baino gehiago uzkurtzen da eta, horrela, uzkurdura diferentziala sartzen da, deformazio edo konketa marka etab. (Plastikoen uzkurdura ezaugarriak eta pvT ezaugarriak).
Hori dela eta, plastikozko piezak diseinatzeko oinarrizko araua dugu; ahal den neurrian hormaren lodierak uniformea edo konstantea izan behar du piezan zehar. Hormaren lodiera horri hormaren lodiera nominala deritzo.
Piezan atal sendoa baldin badago, hutsa egin beharko litzateke nukleoa sartuz. Honek hormaren lodiera uniformea bermatu behar du nukleoaren inguruan.
3) .Zein dira hormaren lodiera erabakitzeko kontuan?
Lanerako nahikoa lodia eta zurruna izan behar du. Hormaren lodiera 0,5 eta 5 mm artekoa izan daiteke.
Gainera, azkarrago hozteko adina mehea izan behar du, ondorioz pisuaren zati txikiagoa eta produktibitate handiagoa lortzen da.
Hormaren lodieraren edozein aldaketa ahalik eta gutxien mantendu behar da.
Hormaren lodiera desberdineko plastikozko piezak hozte-abiadura eta uzkurdura desberdinak izango ditu. Horrelakoetan tolerantzia estua lortzea oso zaila eta askotan ezinezkoa bihurtzen da. Hormaren lodieraren aldakuntza funtsezkoa denean, bien arteko trantsizioa mailakakoa izan behar da.
5. Piezen arteko konexioaren diseinua
Normalean bi maskorrak elkarrekin konektatu behar ditugu. Hauen artean gela itxi bat osatzea barne osagaiak jartzeko (PCB muntaia edo mekanismoa).
Ohiko konexio motak:
1). Atxikitzeko kakoak:
Kakoen konexioa tamaina txikiko eta ertaineko produktuetan erabili ohi da. Bere ezaugarria da kako-kakoak piezen ertzean ezartzen direla eta produktuaren tamaina txikiagoa izan daitekeela. Muntatzen denean, zuzenean ixten da, hala nola bihurkinak, ultrasoinu bidezko soldadura trokelak eta beste. Desabantaila da kako kakoek moldea korapilatsuagoa izan daitekeela. Slider mekanismoa eta altxatzeko mekanismoa beharrezkoak dira kakoen konexioa gauzatzeko eta moldearen kostua handitzeko.
2). Torlojuen junturak:
Torlojuen junturak sendoak eta fidagarriak dira. Bereziki, torlojua + azkoina finkatzea oso fidagarria eta iraunkorra da, desmuntaketa anitz uzten baitu arrakalarik gabe. Torlojuaren konexioa blokeatzeko indar handia eta desmuntatze anitza duten produktuetarako egokia da. Desabantaila da torlojuaren zutabeak leku gehiago hartzen duela.
3). Buruak muntatzea:
Nagusien konexioa bi zati finkatzea da, bossen eta zuloen arteko koordinazio estuaren bidez. Konexio modu hau ez da nahikoa indarra produktuak desmuntatzeko. Desabantaila da blokeatzeko indarra txikitu egingo dela desmuntatzeko denbora handitzen den neurrian.
4). Ultrasoinu bidezko soldadura:
Ultrasoinu bidezko soldadura bi zatiak ultrasoinu moldean jarri eta kontaktu gainazala fusionatuz ultrasoinu bidezko soldaduraren makinaren eraginez egiten da. Produktuaren tamaina txikiagoa izan daiteke, injekzioko moldea nahiko erraza da eta konexioa sendoa da. Desabantaila ultrasoinu molde eta ultrasoinu bidezko soldadura makina erabiltzea da, produktuaren tamaina ezin da handiegia izan. Desmuntatu ondoren, ultrasoinu piezak ezin dira berriro erabili.
6. Azpimutikoak
Azpimarrak moldearen erdia kentzea oztopatzen duten elementuak dira. Azpimarrak diseinuko edozein lekutan ager daitezke. Hauek onartezinak dira, zati batean angelu zirriborrorik ez izatea baino okerragoak badira. Hala ere, azpimarragarri batzuk beharrezkoak edo / eta saihestezinak dira. Kasu horietan, beharrezkoa
mozketak moldean piezak irristatuz / mugituz sortzen dira.
Gogoan izan mozketak sortzea moldea ekoizterakoan garestiagoa dela eta gutxienekoa izan behar dela.
7. Onartzen saiheskiak / Gussets
Plastikozko ataleko saihetsek piezaren zurruntasuna (kargaren eta piezaren desbideraketaren arteko harremana) hobetzen dute eta zurruntasuna areagotzen dute. Molde gaitasuna ere hobetzen du, urtzen saihesbidea norabidean azkartzen baitute.
Saihetsak piezaren itxura ez duten gainazaletan tentsio eta desbideratze maximoren norabidean kokatzen dira. Moldeak betetzeak, uzkurtzeak eta kanporatzeak ere saihetsak jartzeko erabakietan eragin behar dute.
Horma bertikalarekin bat egiten ez duten saihetsak ez dira bat-batean amaitu behar. Horma nominalera pixkanaka igarotzeak estresa kontzentratzeko arriskua murriztu beharko luke.
Saihetsa - neurriak
Saihetsek dimentsio hauek izan beharko lituzkete.
Saihetsen lodierak hormaren lodiera nominala 0,5 eta 0,6 aldiz artekoa izan behar du harraska marka saihesteko.
Saihetsaren altuerak 2,5 edo 3 aldiz hormaren lodiera nominala izan behar du.
Saiheskiak 0,5 eta 1,5 gradu arteko angelua izan behar du kanporatzea errazteko.
Saihetsaren oinak 0,25 eta 0,4 aldiz erradioa izan behar du hormaren lodiera nominala.
Bi saihetsen arteko distantziak hormaren lodiera nominala 2 edo 3 aldiz (edo gehiago) izan behar du.
8. Erradiatutako ertzak
Bi gainazal elkartzen direnean, izkin bat osatzen du. Izkinan, hormaren lodiera hormaren lodiera nominala 1,4 aldiz handitzen da. Honek uzkurdura diferentziala eta moldatutako tentsioa eta hozte denbora luzeagoa lortzen ditu. Beraz, zerbitzuan huts egiteko arriskua handitzen da izkin zorrotzetan.
Arazo hau konpontzeko, izkinak erradioarekin leundu behar dira. Erradioa kanpotik eta barnetik eman behar da. Ez ezazu sekula barneko izkin zorrotzik arrakala sustatzen baitu. Erradioak hormaren lodiera etengabeko araua berresten dutela izan behar du. Hobe da izkinetan hormaren lodiera 0,6 eta 0,75 arteko erradioa izatea. Ez ezazu sekula barneko izkin zorrotzik arrakala sustatzen baitu.
9. Torlojuaren buruaren diseinua
Bi torloju erabiltzen ditugu beti bi erdi kasu elkarrekin konpontzeko edo plastikozko piezen gainean PCBA edo beste osagai batzuk lotzeko. Beraz, torlojuen buruak piezak finkatzeko eta finkatzeko egitura dira.
Torlojuaren buruak forma zilindrikoa du. Nagusia oinean amarekin lotu daiteke edo alboan lotu daiteke. Alboan estekatzeak plastikozko atal lodia eragin dezake, ez da komenigarria, harraska marka eragin dezake eta hozte denbora handitu. Arazo hau konpondu daiteke zirriborroa alboko paretarekin saiheskian lotuz zirriborroan agertzen den moduan. Nagusia zurrun bihur daiteke kontrahorma saihetsak emanez.
Torlojua nagusiari beste zati bat lotzeko erabiltzen da. Hariak eratzeko torlojuak eta errodadura mozteko torlojuak daude. Hariak osatzeko torlojuak termoplastikoetan erabiltzen dira eta haria mozteko torlojuak plastikozko pieza termoegonkor inelastikoetan erabiltzen dira.
Hariak eratzeko torlojuek emearen hariak sortzen dituzte bossaren barruko paretan hotz-fluxuaren bidez - plastikoa moztu baino gehiago deformatu egiten da.
Torlojuaren buruak dimentsio egokiak izan behar ditu torlojua sartzeko indarrak eta zerbitzuan torlojuan jarritako karga jasateko.
Zuloaren tamaina torlojuarekiko kritikoa da haria kentzeko eta torlojua ateratzeko erresistentzia lortzeko.
Bossaren kanpoko diametroak nahikoa handia izan behar du haria sortzearen ondorioz uztai tentsioak jasateko.
Zuloak diametroa zertxobait handiagoa du sarrerako hutsunean luzera laburrean. Horrek torlojua kokatzen laguntzen du sartu aurretik. Nagusiaren mutur irekian dauden tentsioak ere murrizten ditu.
Polimeroen fabrikatzaileek beren materialen buruaren dimentsioa zehazteko jarraibideak ematen dituzte. Torlojuen fabrikatzaileek torlojuaren barren tamaina egokia lortzeko jarraibideak ematen dituzte.
Kontuz ibili behar da torlojuaren sasoi inguruan soldadura-juntura sendoak bermatzeko.
Kontuz ibili behar da ugazaban moldatutako estresa saihesteko, ingurune erasokorrean huts egin dezakeelako.
Nagusiaren zulaketak hari sakonera baino sakonagoa izan behar du.
10. Azaleko dekorazioa
Batzuetan, itxura ona izateko, plastikozko zorroaren azalean tratamendu berezia egiten dugu maiz.
Hala nola: ehundura, distira handikoa, spray pintura, laser bidezko grabatua, estanpazio beroa, galbanizazioa eta abar. Beharrezkoa da aldez aurretik produktuaren diseinuan kontuan hartzea, ondorengo prozesamendua ekiditeko edo produktuaren muntaketan eragina duten tamaina aldaketak saihesteko.